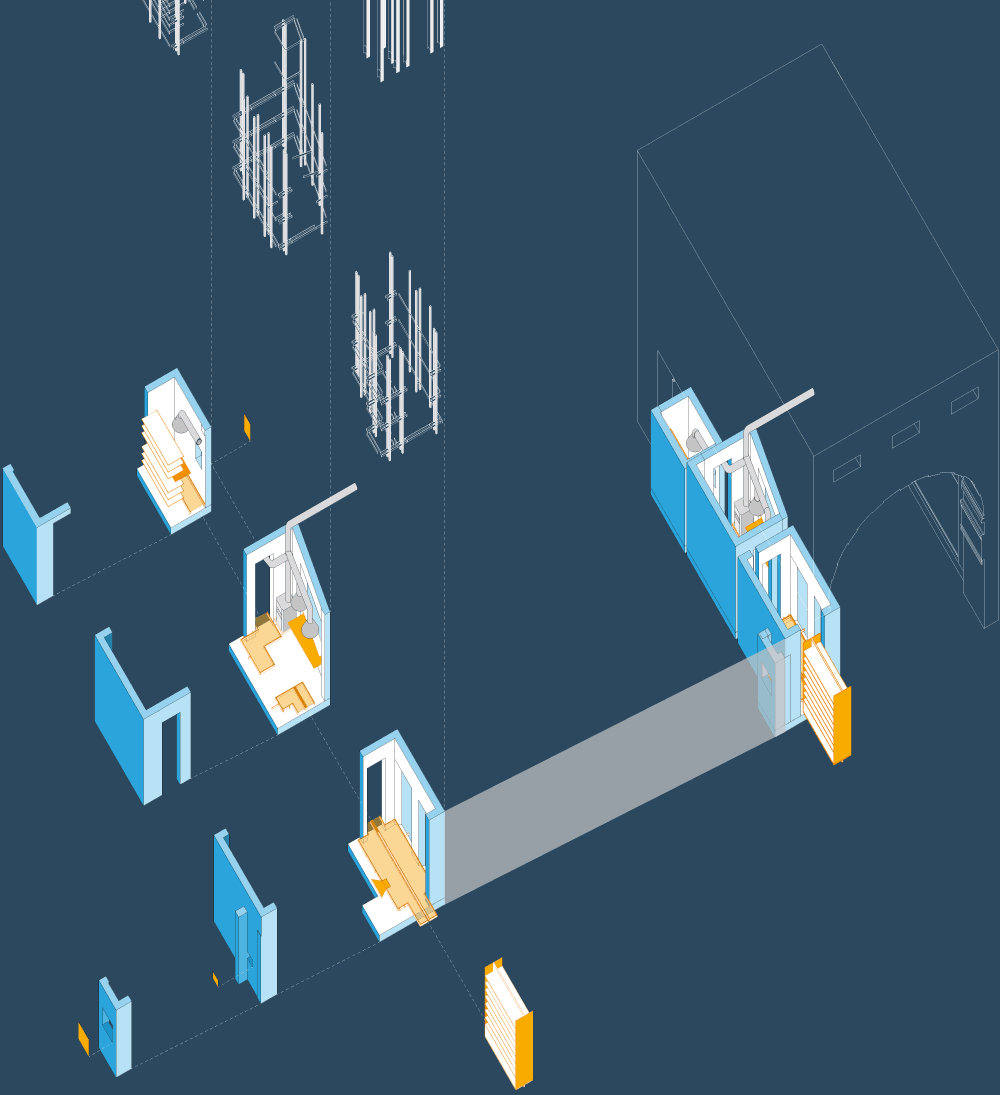
Bioplastics: Screening & Forming
Oxford Brookes School of Architecture · BA Year 3
COMPOSITE WALL
A structural and insulating wall component made from layering two forms of bioplastic and steel reinforcements. Creating an innovative, lightweight and low cost enclosure for use in the Pocket Dyers design project. Incorporating benefits found in traditional rainscreen cladding systems and the use of waste/renewable bioplastic materials.
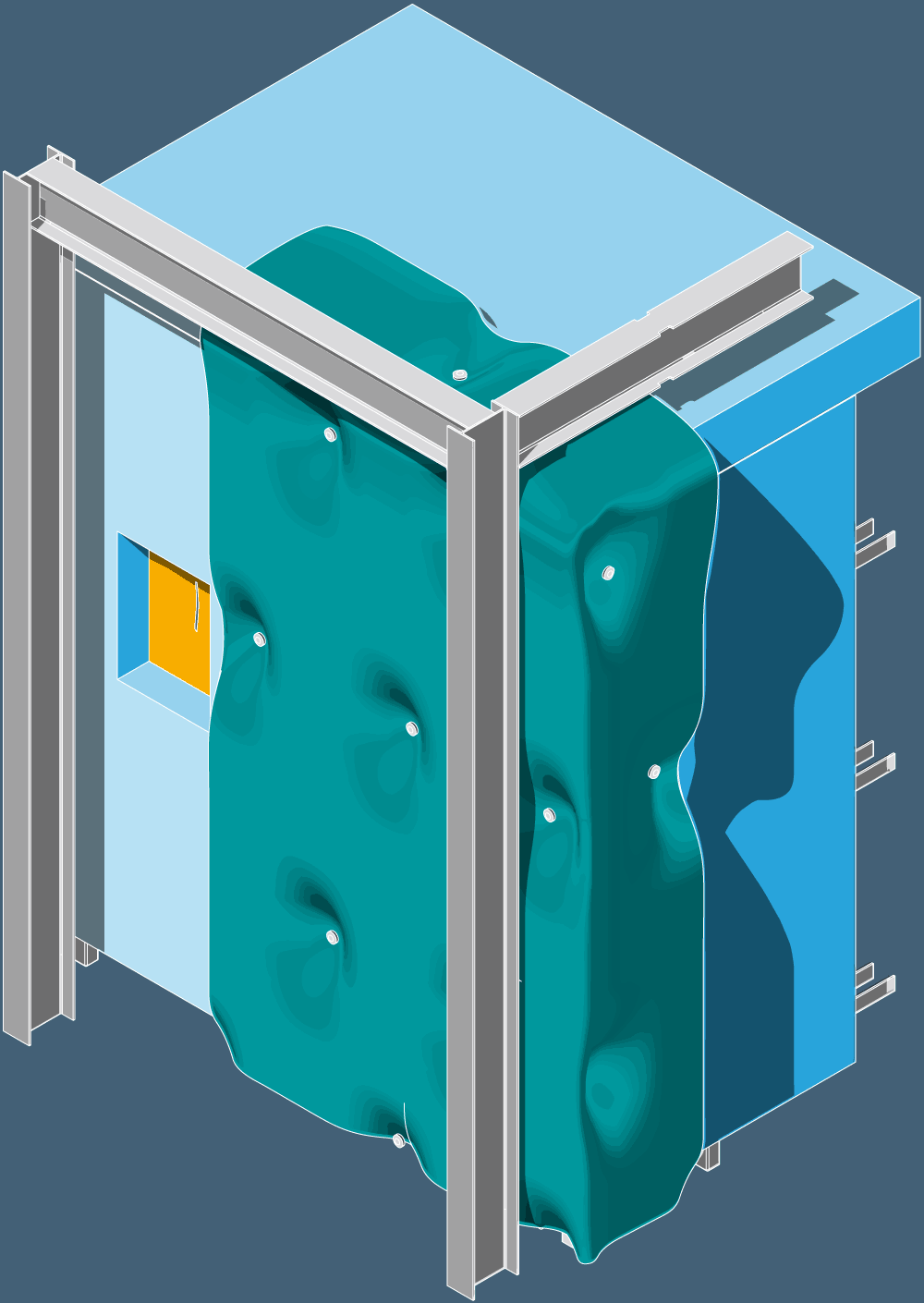
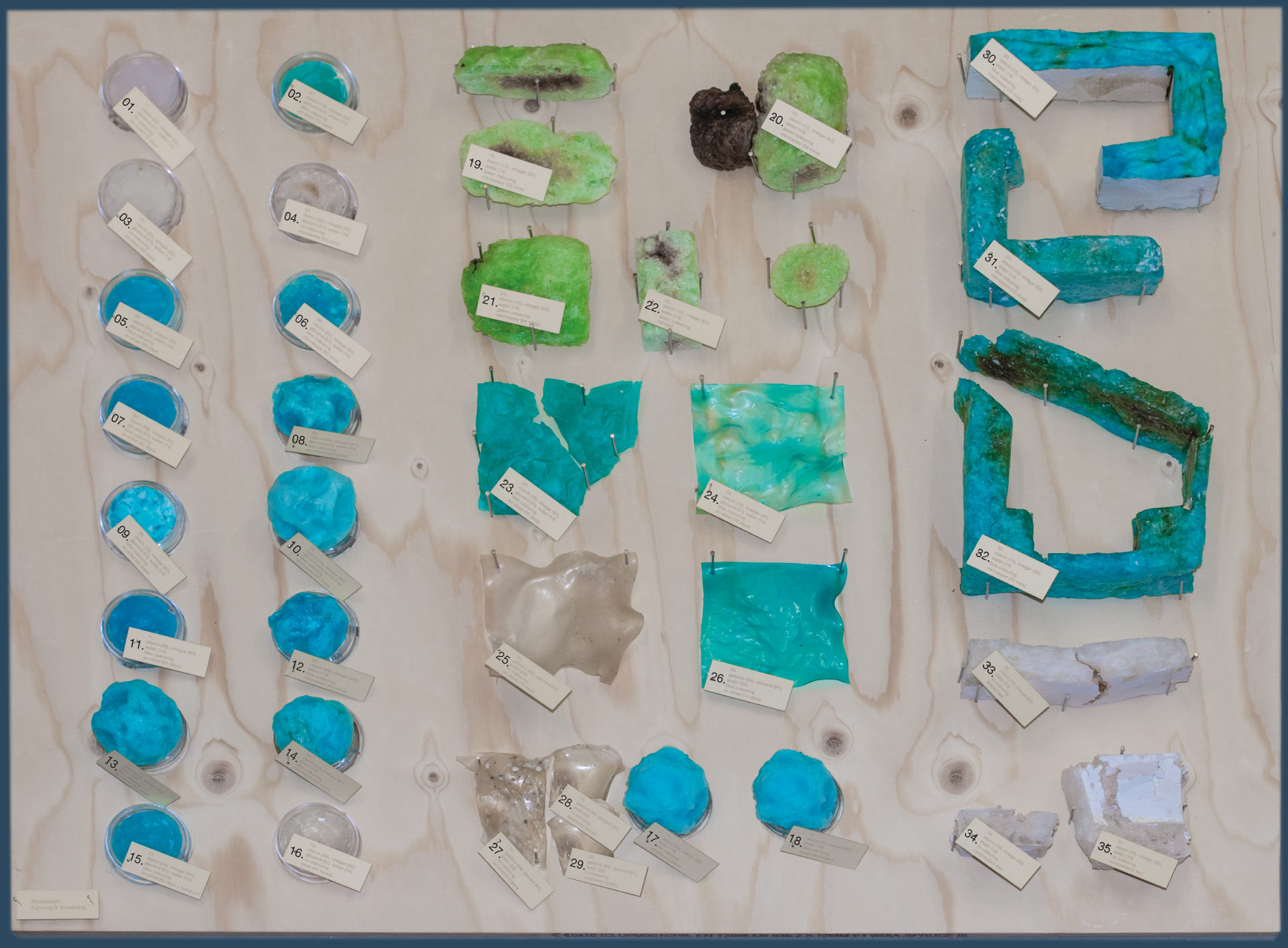
Material Samples
01.
starch (02), vinegar (02), glycerol (01), water (14) no colouring air-dried (10 days) |
02. starch (16), vinegar (02), glycerol (01), water (14) blue colouring air-dried (10 days) |
03. starch (02), vinegar (02), glycerol (01), water (14) no colouring air-dried (03 days) |
04. starch (02), vinegar (02), glycerol (01), water (14) no colouring microwave (03 mins) |
05. starch (04), vinegar (02), glycerol (01), water (14) blue colouring air-dried (03 days) |
06. starch (04), vinegar (02), glycerol (01), water (14) blue colouring microwave (03 mins) |
07. starch (08), vinegar (02), glycerol (01), water (14) blue colouring air-dried (03 days) |
08. starch (08), vinegar (02), glycerol (01), water (14) blue colouring microwave (03 mins) |
09. starch (16), vinegar (02), glycerol (01), water (14) blue colouring air-dried (03 days) |
10. starch (16), vinegar (02), glycerol (01), water (14) blue colouring microwave (03 mins) |
11. starch (08), vinegar (02), water (14) blue colouring air-dried (03 days) |
12. starch (08), vinegar (02), water (14) blue colouring microwave (03 mins) |
13. starch (12), vinegar (02), water (14) blue colouring microwave (03 mins) |
14. starch (12), vinegar (02), water (14) blue colouring microwave (05 mins) |
15. starch (04), vinegar (02), glycerol (01), water (14) blue colouring air-dried (03 days + hair-dryer) |
16. starch (04), vinegar (02), glycerol (01), water (14) no colouring oven (01 hours) |
17. starch (12), vinegar (02), water (14) blue colouring microwave (03 mins) / weathered (water) |
18. starch (12), vinegar (02), water (14) blue colouring microwave (03 mins) / weathered (frozen) |
19. starch (12), vinegar (02), water (14) green colouring microwave (03 mins) |
20. starch (12), vinegar (02), water (14) green colouring microwave (04 mins) |
21. starch (12), vinegar (02), water (14) green colouring microwave (04 mins) |
22. starch (12), vinegar (02), water (14) green colouring microwave (04 mins) / sanded |
23. starch (16), vinegar (02), glycerol (01), water (14) blue colouring air-dried (10 days) |
24. starch (16), vinegar (02), glycerol (01), water (14) blue colouring air-dried (10 days) |
25. gelatine (04), glycerol (01), water (20) no colouring air-dried (14 days) |
26. gelatine (04), glycerol (01), water (20) blue colouring air-dried (14 days) |
27. gelatine (04), glycerol (01), water (20) no colouring air-dried (14 days) |
28. gelatine (04), glycerol (01), water (20) no colouring air-dried (14 days) / weathered (water) |
29. gelatine (04), glycerol (01), water (20) no colouring air-dried (14 days) / weathered (frozen) |
30. starch (12), vinegar (02), water (14) blue colouring microwave (15 mins) |
31. starch (12), vinegar (02), water (14) blue colouring microwave (15 mins) |
32. starch (12), vinegar (02), water (14) blue colouring microwave (20 mins) |
33. starch (12), vinegar (02), water (14) no colouring tension test |
34. starch (12), vinegar (02), water (14) no colouring compression test |
35. starch (12), vinegar (02), water (14) no colouring compression test |
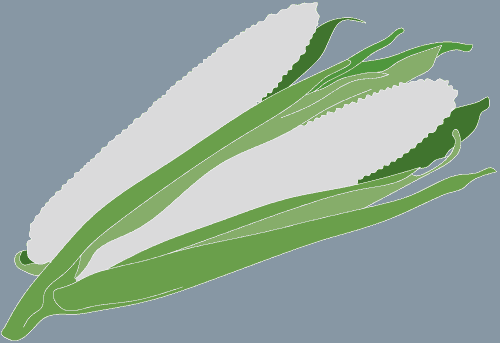
Bioplastics are plastics from renewable biomass sources, such as vegetable fats, corn starch or animal products. Traditional plastics are primarily derived from petroleum and produce more greenhouse gas.
Bio-Polymer(s) + Bio-Plasticizer(s) + Other Additive(s) = Bio-Plastic
The starch/gelatine is the polymer. Polymers are large chains of molecules like plastics, the acidic vinegar + heat breaks down polymers which then reform when drying. Glycerin makes the plastic more flexible and soft.
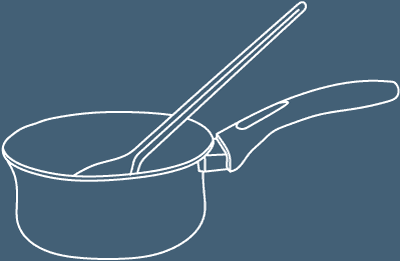
MAKING
GELATINE · SCREENING
Combine the gelatine, glycerin, water and colouring then heat gently until frothing. Remove from the heat and continue to stir. Pour into a flat mould and leave to air dry. Can be shaped while semi-dry.
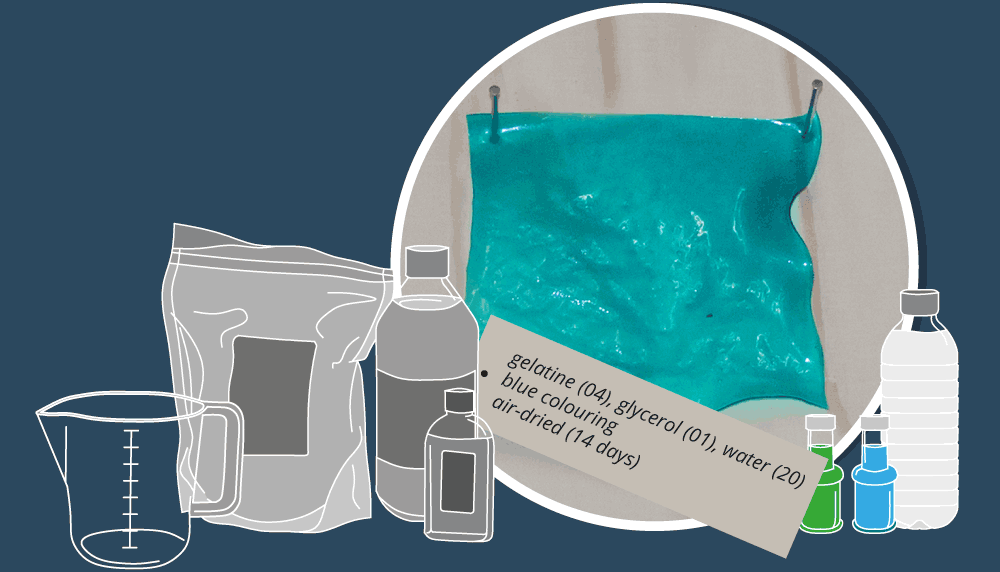
FAILURES
Microwave overheating starts to burn the inside of the plastic and the centre can explode outwards. Oven heating/drying is hard to control and results in partially dry samples, while air drying starch tends to crack.
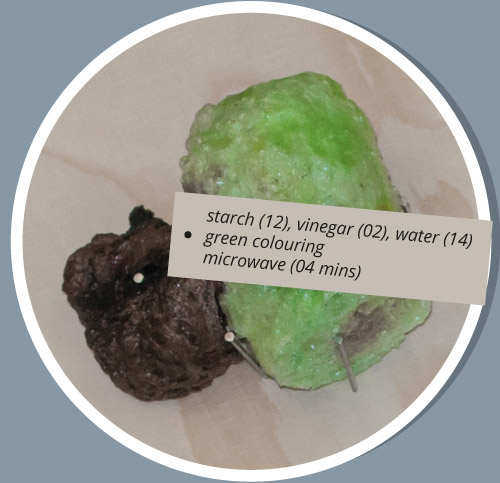
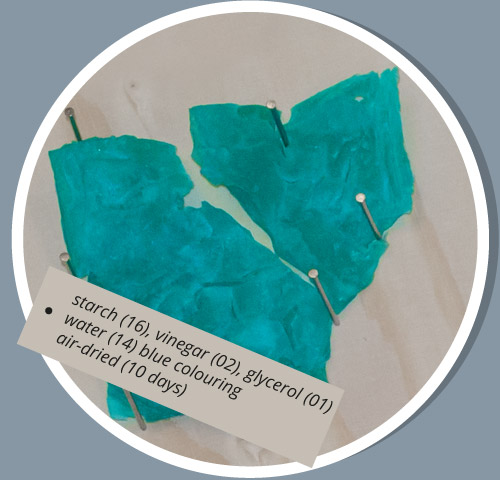
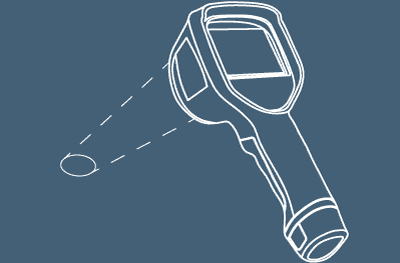
TESTING

plasterboard
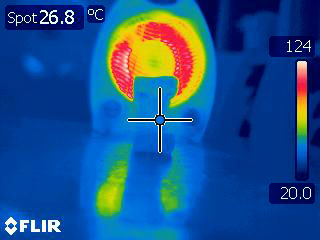
bioplastic
THERMAL
A basic thermal conduction comparison using a FLIR thermal camera between plasterboard and starch based bioplastic. The air cells of the starch bioplastic caused a transfer reduction of 7°C.
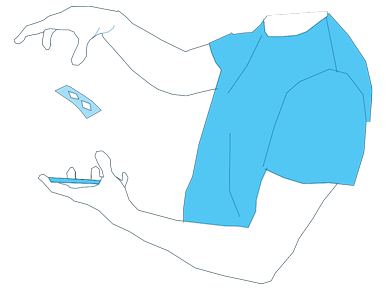
TUTORS Johan Hybschmann, Matthew Springett, Maria Kessler & Margaret Bursa
2014-15
© Theo Jones · Creative Commons